在技術中心有這樣一組專屬數字,“14213”。這組數字概括了公司推行研發設計工藝一體化以來取得的一系列成績,也是打造太重標準、提升太重質量、樹立太重品牌的一組密碼——截至目前,中心總體設計改進106項,批量產品累計制造49臺,單件小批量產品研發設計27臺,配套零部件產品工藝優化12項,鑄鍛件產品制造完成370噸。
今年,公司科技質量大會和公司黨委中心組(擴大)專題學習會多次強調,要按照研發設計工藝一體化、制造采購安調一體化、工藝質量檢驗一體化管理思路,推動產品設計、營銷、管理標準化、系列化、模塊化、平臺化。
按照公司《研發設計工藝一體化工作方案》要求,技術中心全面推進研發設計與工藝的相互融合,以全方位服務生產制造需求為主線,根據批量型、單件小批量、配套零部件和鑄鍛件四種不同類型產品的設計制造特點,制定了四類不同產品實施計劃,明確時間表、責任人、路線圖,工藝設計、研發制造成果顯著。
研發設計
以服務生產產線和生產工序為主線,技術中心按產線工位需求,共進行了106項精細化設計,如優化圖紙層級、補充工藝信息、固化電氣及液壓管路走線、裝夾定位工裝等。不僅暢通了生產流程,還實現了降本增效。
批量化產品
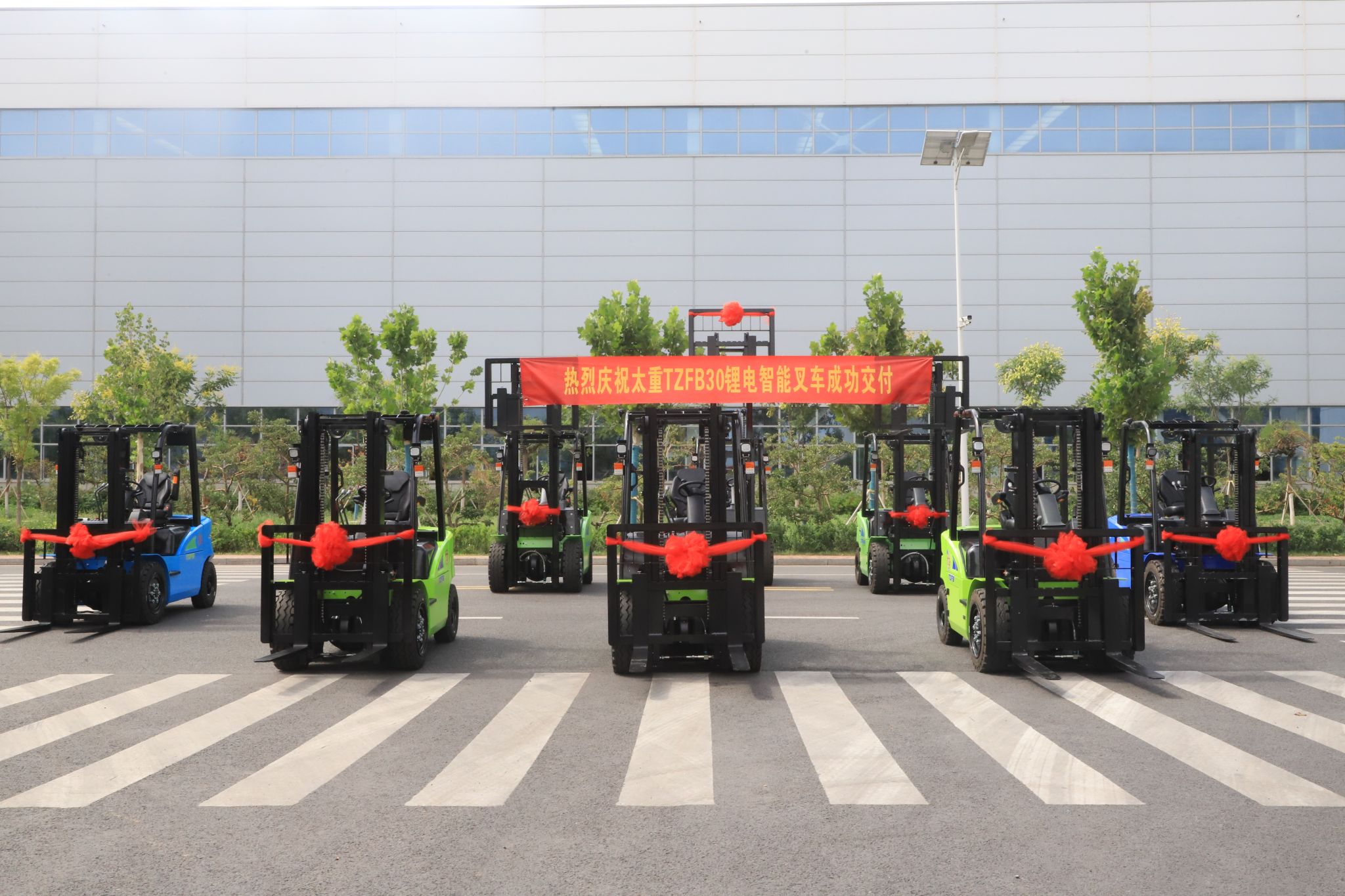
技術中心從設計源頭進行研發設計工藝一體化規劃,在寬體車、叉車、剪叉式高空作業平臺等批量化產品上穩步推進,結合產線工藝流程、產品特點和工位布局,圍繞圖紙層級優化、模塊化設計、工藝信息上圖紙、管路布局優化等方面展開工作,生產效率明顯提升,產品質量有效改善,制造成本持續降低,批量化產品的核心競爭力大大增強。當前,共49臺批量化產品制造完成。
單件小批量產品
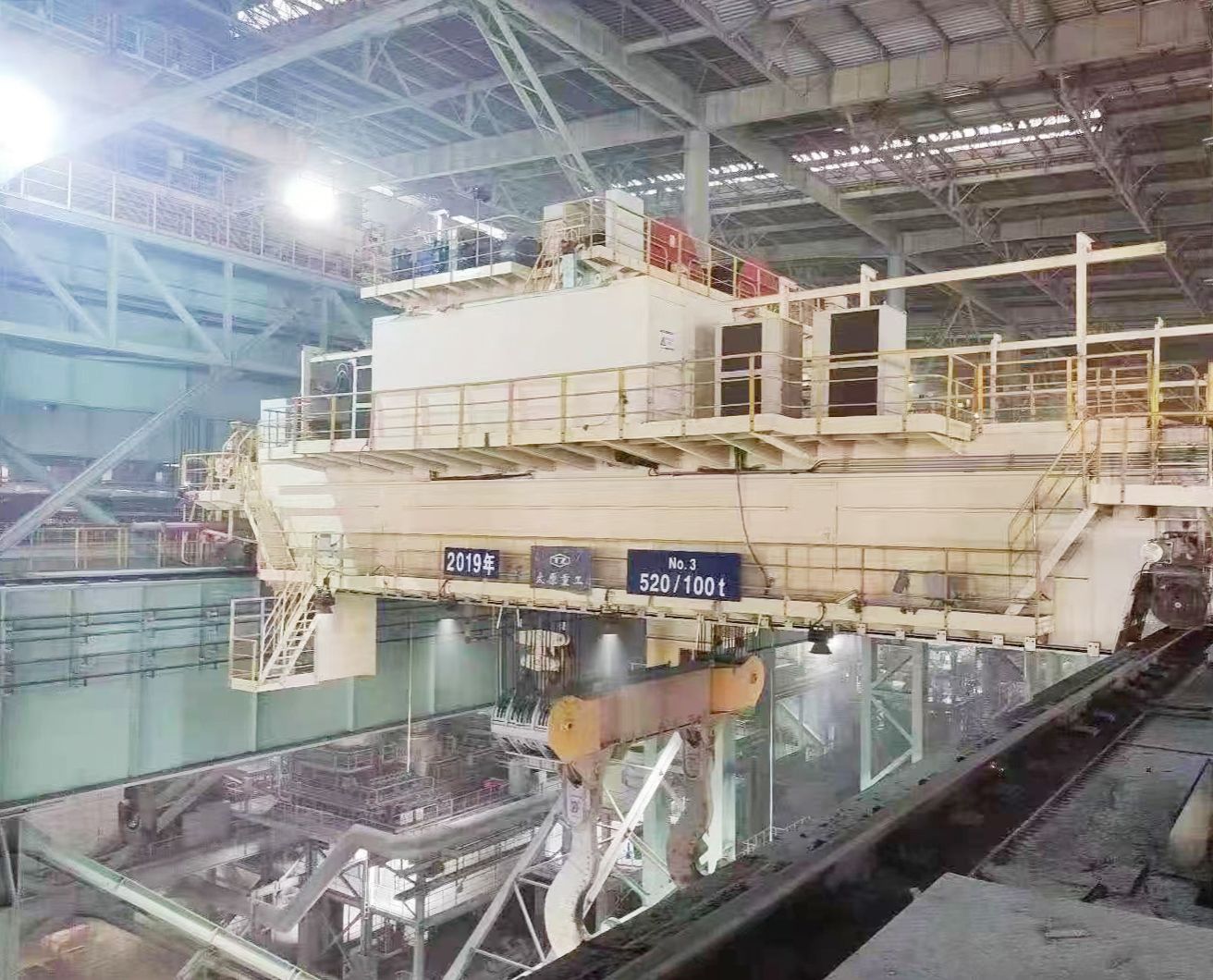
圍繞生產服務、精細設計和降本增效等方面,技術中心積極推進研發設計工藝一體化工作。以起重機產品為例,面對主梁超長板對接拼焊不規范的問題,設計人員結合公司采購標準板材規格,制定了起重機主梁板材拼接規范,從設計端明確標注超長板的焊縫位置和焊縫形式,提高了板材利用率,保證了主梁焊接質量。三個月時間,包括起重機、矯直機在內,共27臺單件小批量產品完成研發設計改進工作。
配套零部件產品

配套零部件直接影響著整機設備的質量和性能。在配套零部件產品改進方面,技術中心齒傳專業選取公司重點產品配套減速機作為試點,以問題為導向,提出解決措施,先后開展了螺栓力矩標注、增加產品結構改進、模塊化設計等12項工藝融合工作,齒輪箱產品質量明顯改善。
鑄鍛件產品
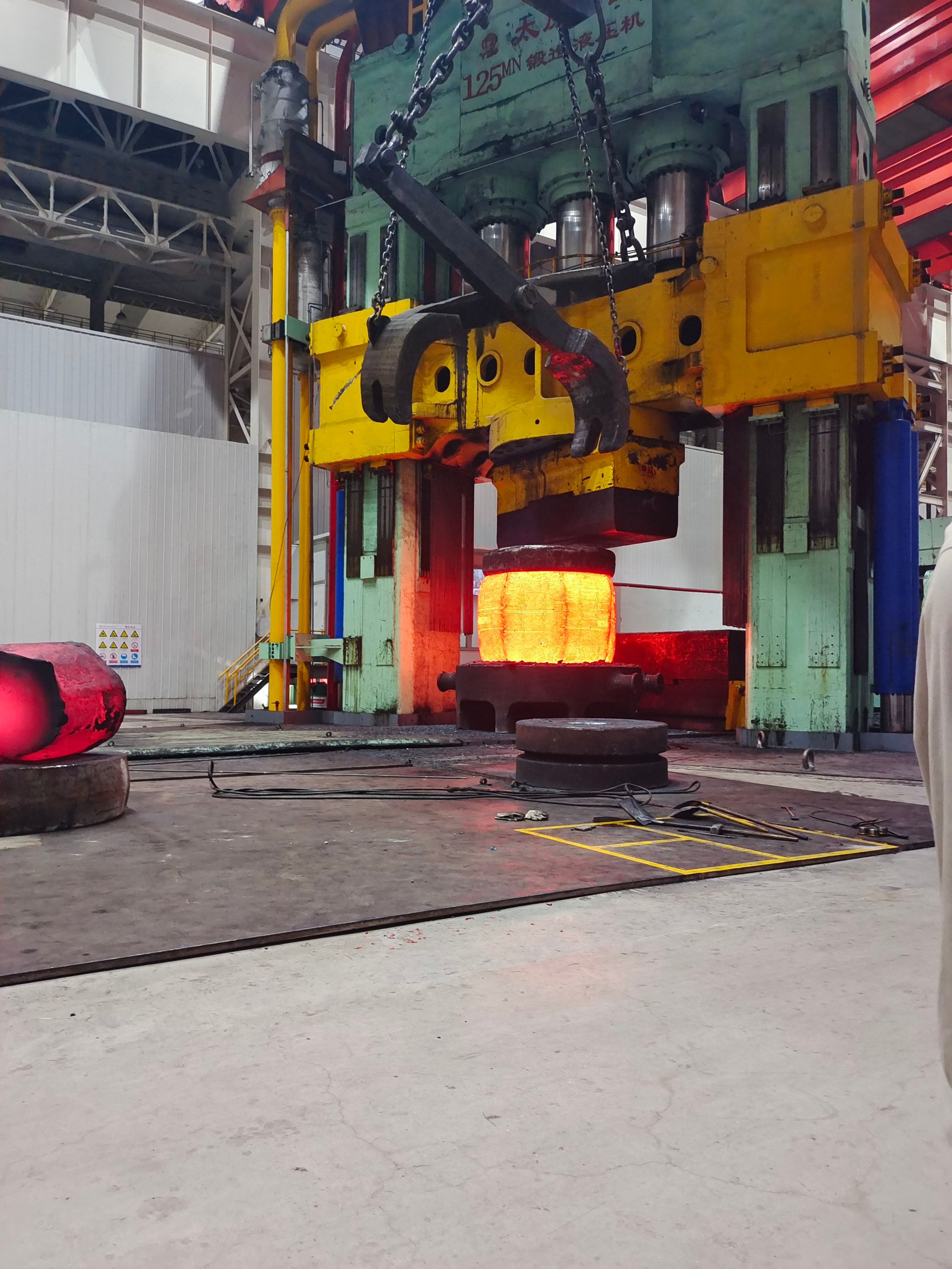
技術中心熱工所在模具鋼的開發制造過程中,從材料成分優化、鍛造工藝和熱處理等方面入手,驗證鑄鍛件產品研發設計工藝一體化工作思路和方法,建立規范化設計體系,實現了質量、效率和成本控制的全面提升。截至目前,370噸鑄鍛件產品制造完成。
在圍繞具體產品開展工作的同時,技術中心還注重技術人員的能力培養和提升,針對性地制定年度培訓計劃,要求工藝技術專家對設計人員進行焊接、機加工、裝配、工藝裝備等工藝基礎知識培訓,現已累計開展培訓106課時。通過工藝培訓,增強了設計人員對生產裝備和制造工藝的全面了解,將工藝知識陸續運用到產品設計中,從而對設計工藝融合有了更加深刻的認識,產品設計的精細化水平明顯提高。
未來,技術中心將認真總結經驗做法,繼續鞏固和擴大工作成果,以點帶面形成輻射引領,徹底打破設計工藝壁壘,全面提升產品質量、生產效率和成本管控水平,為把太重真正打造成為跨越時空、基業長青、朝氣蓬勃的百年老店貢獻技術力量!